Fasteners and Machining: Streamlining the Production Process
Fasteners and Machining: Streamlining the Production Process
Blog Article
Unveiling the Intricacies of Bolts and Machining Processes for Ideal Performance
In the world of engineering and manufacturing, the option of fasteners and the intricacies of machining procedures play a critical duty in establishing the utmost performance and resilience of an item. From the relatively straightforward job of selecting the right kind of fastener to the facility precision machining methods utilized, every action in this procedure demands careful attention to information. As we start this expedition right into the world of bolts and machining, we will reveal the subtle yet critical aspects that can considerably influence the efficiency and top quality of the end product, clarifying the usually neglected aspects that can make all the distinction in achieving ideal efficiency.
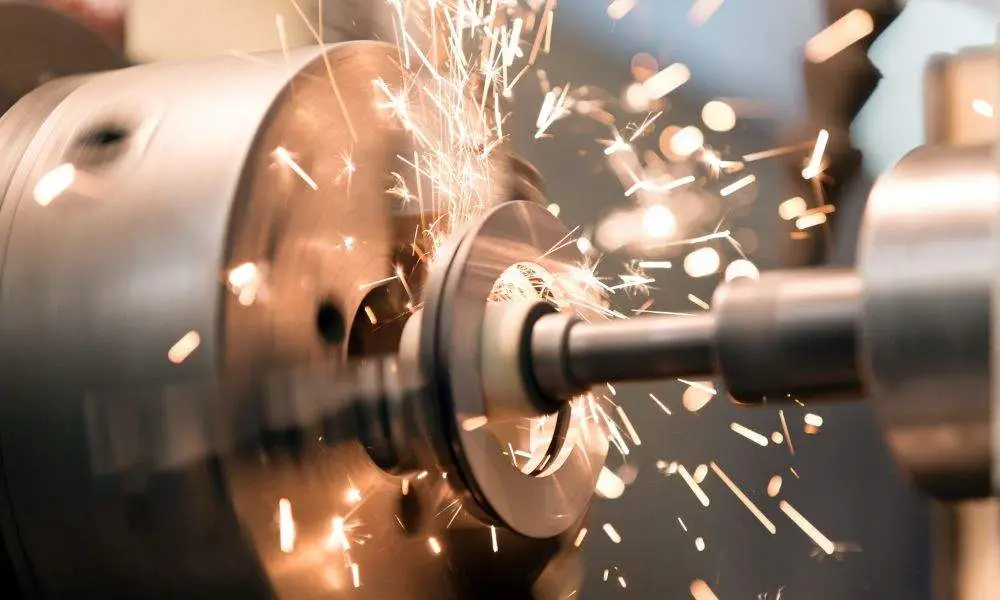
Significance of Appropriate Bolt Option
Choosing the suitable bolts is important in making sure the structural integrity and long life of any type of mechanical assembly. Bolts play a fundamental duty in holding components together safely, with the ideal selection contributing dramatically to the total efficiency and dependability of the setting up. When choosing bolts, elements such as material compatibility, environmental conditions, load-bearing capacity, and simplicity of installation should be thoroughly considered to ensure optimal efficiency.
Improper bolt choice can cause a variety of issues, consisting of loosening, rust, and even structural failing. Utilizing bolts that are not fit to the specific needs of the assembly can endanger its performance and posture security threats. For that reason, designers and designers should meticulously examine the application needs and select fasteners that fulfill or exceed the required criteria and specifications.
Furthermore, the appropriate bolt option process entails assessing the joint design, expected lots, resonance levels, and potential thermal growth or tightening to make certain that the picked fasteners can endure the operating problems efficiently. By prioritizing appropriate bolt option, suppliers can enhance the quality, toughness, and efficiency of their mechanical settings up.
Kinds and Characteristics of Bolts
A necessary facet of mechanical settings up depends on understanding the diverse types and unique qualities of fasteners used in different industrial applications. Fasteners are important elements that hold structures together, making sure stability and performance. There is a variety of fasteners available, each designed for specific functions based on the application demands. Common kinds of fasteners consist of screws, bolts, nuts, washers, pins, and rivets.
Screws are threaded bolts that are generally made use of to join 2 or more components with each other. Bolts are comparable to screws however are usually used with a nut to develop a safe joint. Nuts are internally threaded bolts that mate with bolts to hold parts together. Washing machines are thin plates that disperse the tons of a bolt, stopping damage to the product being fastened. Rivets are irreversible fasteners that are hammered or pushed into area. Pins are used for placement or to secure parts temporarily.
Understanding the qualities of each sort of bolt is essential for selecting the ideal one for a certain application, making certain optimum efficiency and dependability of the mechanical setting up. Fasteners and Machining.
Precision Machining Techniques for Efficiency
The intricate design needs of numerous bolts require employing accuracy machining strategies for ideal effectiveness in manufacturing procedures. Precision machining is critical in ensuring that bolts satisfy the precise specs needed for their intended application. Among the main methods made use of in accuracy machining is Computer system Numerical Control (CNC) machining, which enables high degrees of accuracy and repeatability in the manufacturing of bolts. CNC makers can executing complex cuts additional resources and forming operations with minimal human treatment, causing enhanced performance and uniformity in the manufacturing process.
In enhancement to CNC machining, other accuracy techniques such as grinding, milling, and transforming are commonly made use of to accomplish the tight resistances required for bolts. These strategies enable suppliers to create bolts with smooth surface areas, accurate measurements, and high structural stability. By making use of precision machining strategies, producers can improve the top quality of fasteners, decrease product waste, and boost overall manufacturing performance. Moreover, the usage of advanced machining procedures helps guarantee that bolts meet sector standards and client assumptions for efficiency and integrity.

Aspects Influencing Machining Process Efficiency
Numerous variables play a significant role in figuring out the efficiency of machining procedures in the production of bolts. Maximizing these criteria based on the certain needs of the fastener being produced is essential to accomplishing exact and cost-efficient machining.
Machine rigidity and security additionally play an essential role in identifying machining process performance. A stable maker with very little vibrations can improve accuracy and prevent tool wear, causing far better total efficiency. The ability and experience of the device operator can not be underestimated. An experienced operator can make real-time adjustments, troubleshoot concerns successfully, and make sure that the machining process runs efficiently, inevitably impacting the final top look at this website quality of the fastener.
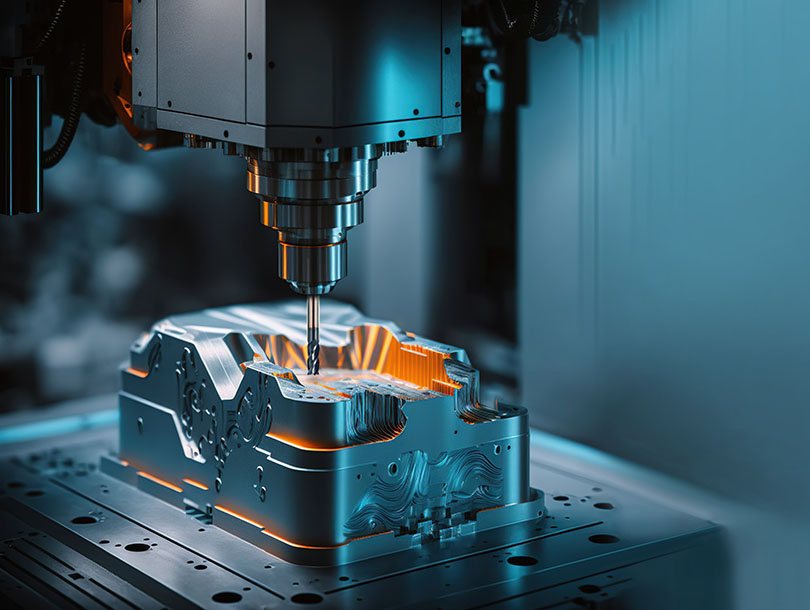
Quality Control Steps in Manufacturing
Elements influencing machining procedure performance, such as reducing device choice and equipment security, straight influence the execution of top quality control steps in manufacturing. Routine upkeep of machining devices is additionally important to copyright top quality control. By sticking to strict top quality control actions, suppliers can boost consumer contentment, construct a track record for dependability, and eventually accomplish ideal performance in their machining processes.
Final Thought
Finally, choosing the best fasteners and utilizing precision machining strategies are essential for ideal performance in making procedures. Recognizing the types and attributes of bolts, along with factors influencing machining process efficiency, can bring about improved effectiveness and quality assurance steps. By taking note of these ins and outs, suppliers can accomplish higher levels of efficiency and reliability in their items.
In the world of design and manufacturing, the choice of bolts and the intricacies of machining procedures play a pivotal browse around this site duty in identifying the supreme performance and longevity of an item (Fasteners and Machining). One of the main strategies made use of in accuracy machining is Computer Numerical Control (CNC) machining, which makes it possible for high levels of precision and repeatability in the production of fasteners. The usage of sophisticated machining procedures helps ensure that bolts meet industry criteria and consumer expectations for efficiency and dependability
In conclusion, selecting the appropriate bolts and utilizing accuracy machining techniques are essential for optimum efficiency in making procedures. Comprehending the types and characteristics of fasteners, along with variables influencing machining process performance, can lead to boosted efficiency and top quality control procedures.
Report this page